El proveedor alemán estrenó un centro de impresión en metal que pretende establecer nuevos estándares en la producción a gran escala y en volumen.
Bosch ya se jacta de ser el primer proveedor europeo Tier-1 que tendrá una instalación para la producción en serie de repuestos, desde carcasas hasta bloques de motor. Velocidad, precisión, flexibilidad y eficiencia energética: para Bosch, estos factores son clave a la hora de fabricar las complejas piezas metálicas que suministra a sus clientes internos y externos. Con una nueva impresora 3D de metal en su planta de Núremberg, Bosch quiere reforzar su papel pionero en la industria de proveedores. De hecho, es el primer proveedor automovilístico europeo que cuenta con una instalación de esta clase de rendimiento. La planta ha invertido casi seis millones de euros en el centro y en la compra e instalación asociadas de una impresora 3D de metal Nikon SLM Solutions NXG XII 600.
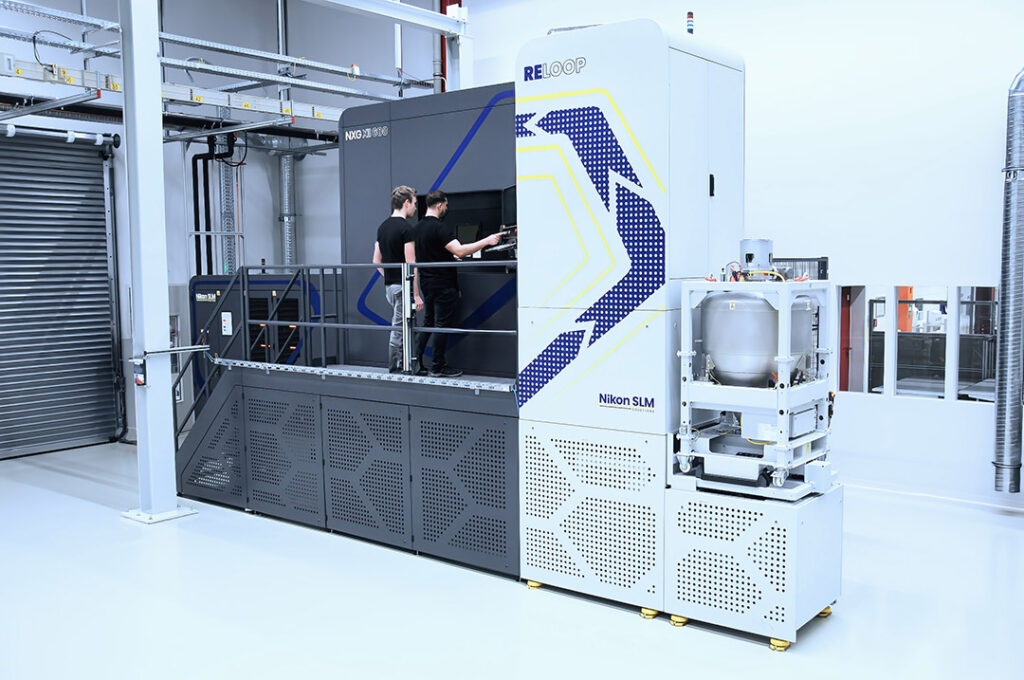
“Bosch sigue apostando por Alemania como emplazamiento industrial e invierte aquí grandes sumas de dinero. Con la introducción de nuevas tecnologías en nuestras plantas, nos aseguramos un considerable potencial de ventas”, afirmó Klaus Mäder, miembro de la junta directiva del sector Bosch Mobility responsable de las operaciones, incluyendo todas las plantas del mundo.
Todo más rápido
Con la nueva impresora 3D se pretende acelerar los ciclos de desarrollo, especialmente en el caso de las piezas metálicas, cuya fabricación requiere mucho tiempo con los procesos de fabricación convencionales. Alexander Weichsel, director de la planta comercial de Núremberg, ponderó la puesta en marcha oficial de la instalación: “Al hacer más rápida y productiva la fabricación de piezas metálicas, esta nueva instalación aumentará nuestra competitividad”. En tanto, el director técnico de la planta, Jörg Luntz, rubricó su alcance. “Con esta instalación, estamos estableciendo los más altos estándares en impresión 3D de metal. En la producción en serie, esto nos abrirá posibilidades completamente nuevas”.
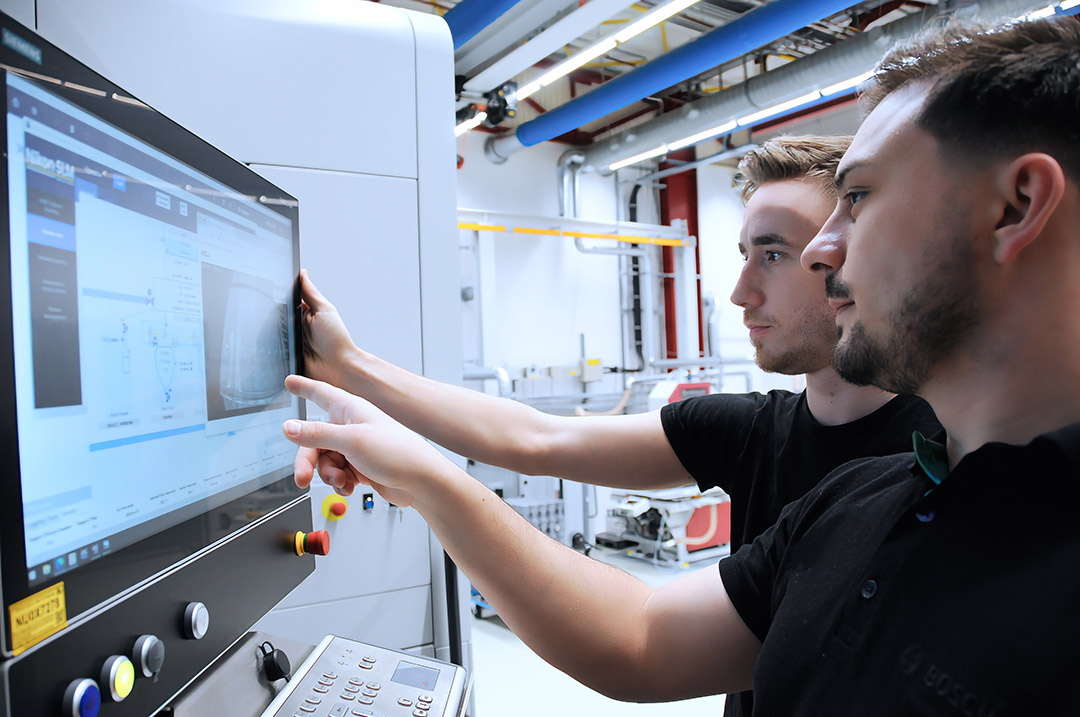
Ya se trate de componentes para aplicaciones de hidrógeno, carcasas de motores para coches eléctricos, componentes para ejes eléctricos o bloques de motor para carreras: el tamaño y las capacidades técnicas de la instalación allanan el camino para un sinfín de aplicaciones. A partir de un archivo de diseño asistido por ordenador desarrollado previamente, sus doce láseres funden el polvo metálico capa por capa para crear formas muy complejas.
Conservación de recursos
La nueva impresora 3D de metal es hasta cinco veces más rápida que los sistemas de impresión 3D utilizados hasta ahora. Estructuras complejas como canales interiores o curvos, que simplemente no son factibles con los procesos de fresado convencionales, pueden producirse ahora sin ningún problema. Mientras que con los métodos convencionales no es posible taladrar las esquinas, la impresión en 3D facilita esta tarea.
La impresora puede producir piezas inacabadas bajo demanda sin necesidad de utillaje. Como la impresión 3D reduce casi a cero el desperdicio de materias primas, también conserva recursos. “El uso de la impresora 3D para fabricar componentes no sólo aumenta la sostenibilidad de la producción, sino que también permite a Bosch responder con flexibilidad a las fluctuaciones en el tamaño de los lotes y ofrecer todo de una sola fuente”, dice Weichsel.
Un paso menos
Un ejemplo especialmente vívido de las nuevas posibilidades que abre el proceso de impresión 3D es el bloque de motor: con la fabricación convencional, se puede tardar hasta tres años en pasar del primer borrador de diseño a la producción en serie. Completar el molde de fundición para el bloque del motor puede llevar hasta 18 meses. La impresión 3D elimina este paso. Los datos del diseño se transmiten directamente a la impresora, lo que elimina la necesidad de moldes complejos. La impresora 3D entrega un bloque de motor acabado en unos pocos días, lo que reduce considerablemente el tiempo total de desarrollo del producto.
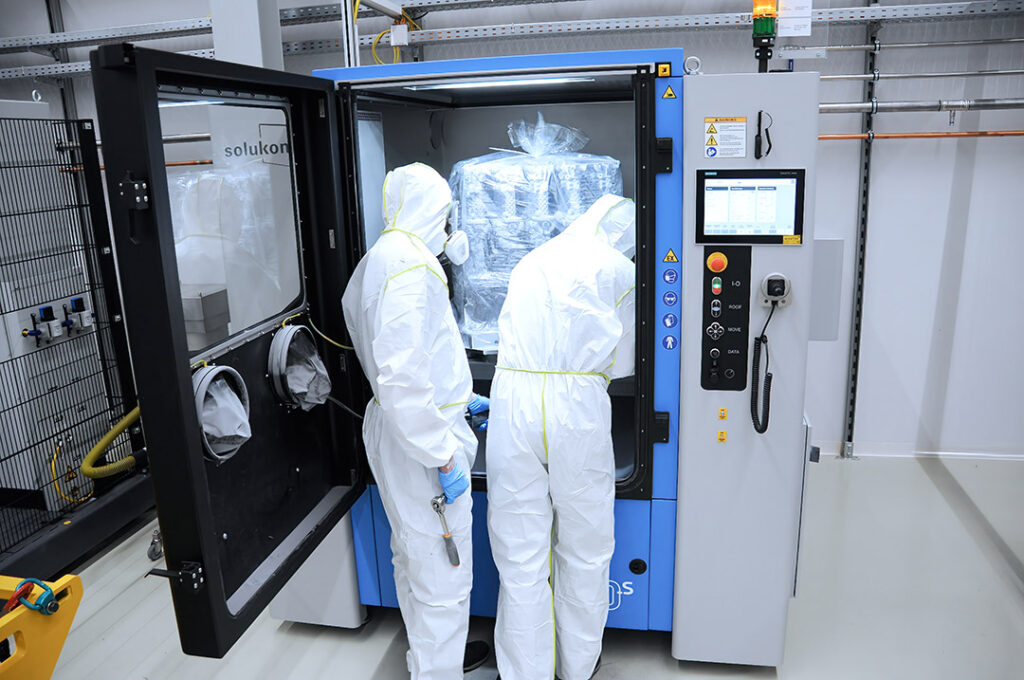
A pleno rendimiento, las instalaciones pueden producir piezas metálicas con un peso total de unos 10.000 kilogramos en menos de un año, alcanzando velocidades de hasta 1.000 centímetros cúbicos por hora. El principal objetivo de esta producción más rápida de componentes es reducir el plazo de comercialización.
“Queremos ser más rápidos que con los procesos de fabricación tradicionales y utilizar esta tecnología para sacar los productos al mercado con mayor rapidez”, afirmó Luntz. “Incluso hoy en día, sólo unas pocas empresas pueden producir tecnología a escala industrial de la forma en que lo hace Bosch. “Ahora vamos un paso más allá, llevando la producción en volumen en impresión 3D sobre metal al nivel de la automoción”. Esto abre la puerta a oportunidades y posibilidades completamente nuevas, en el sector de la automoción, pero también en otras muchas industrias, como la energía y la aviación.